Advanced robotics and hydro-powered smelters: How we build a Polestar
Historically, factories might not have been something you bragged about. Dirty, old, dark buildings, far away from the essence of a company’s brand. But times change. The next generation of automotive manufacturing sites are intelligent, innovative, and green. As the first wave of Polestar 4s roll out of our state-of-the-art facilities (and with Polestar 3 production just around the corner), we’re opening the doors to some of our current and future sites around the world. So, come with us and see what goes into building a high-performance, exclusive electric vehicle.
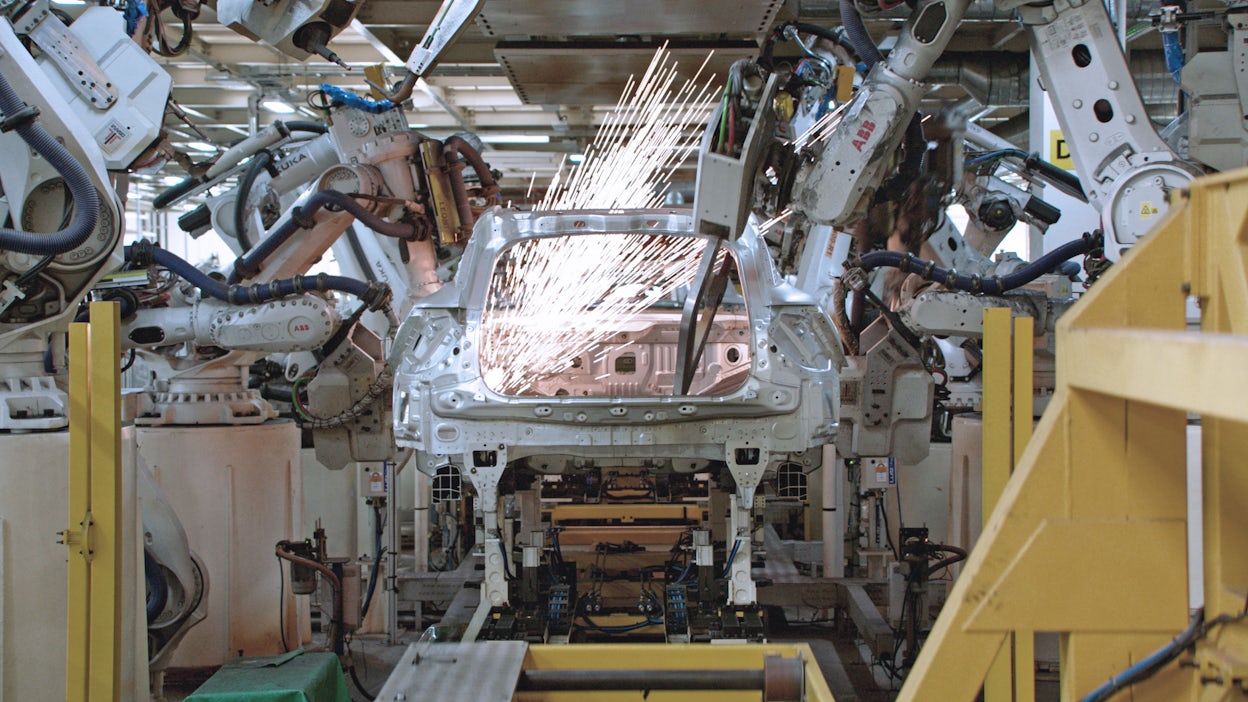
Car manufacturing can be an intricate process. But manufacturing high-performance, next-generation cars is something altogether different. With vehicle-to-grid charging capabilities, advanced driver assistance systems, and an assortment of other cutting-edge car technology under the hood, our latest range of SUVs are some of the most sophisticated vehicles in production today. This mix of technological complexity – coupled with a premium build philosophy – creates a unique manufacturing environment in which to build a car.
Robots and big data
“You're looking at one of the most advanced automotive facilities on the planet,” says Chunlin Zhao, Head of Hangzhou Bay facility. And it’s true. Since opening in 2021, the Hangzhou Bay facility has quickly established itself as one of the region's most impressive car manufacturing plants, capable of producing 300,000 vehicles annually.
Currently responsible for Polestar 4 production, the facility is no stranger to pioneering technology, using a mixture of robots, big data, and artificial intelligence to ensure vehicles retain a premium build and improve the overall efficiency of the manufacturing process. The site boasts over 3,000 inspection points across the production line, meaning comprehensive checks are in place throughout production. With safety forming the centerpiece of our design and manufacturing objectives, nothing is left to chance. “We have a reputation for implementing some of the latest technological advancements into our facilities. If we see something that can improve our processes, we'll look for ways to include this in our sites," explains Chunlin Zhao.
This isn’t just lip service. The welding shop, known locally as the “dark factory” (which isn't quite as scary as it sounds and points to its ability to operate without human intervention), has over 800 fully automated flexible robots capable of performing ultra-complex (but highly repetitive) tasks. The data room turns an endless stream of information into actionable insights. Is the factory running low on a particular item? Which robots require maintenance? These kinds of questions are all handled in real time by advanced analytic systems.
And then there’s the production line, home to the advanced mega-casting equipment that makes large sections of a vehicle from molten aluminum. Although this technology is not currently used in the Polestar line-up, it illustrates the forward-thinking ambitions of the facility. “You can find technology here that you won't find anywhere else in the world,” finishes Chunlin Zhao.
But while robots and big data give the facility a distinctly futuristic feel, its sustainability credentials ensure its roots are firmly planted in the ground.
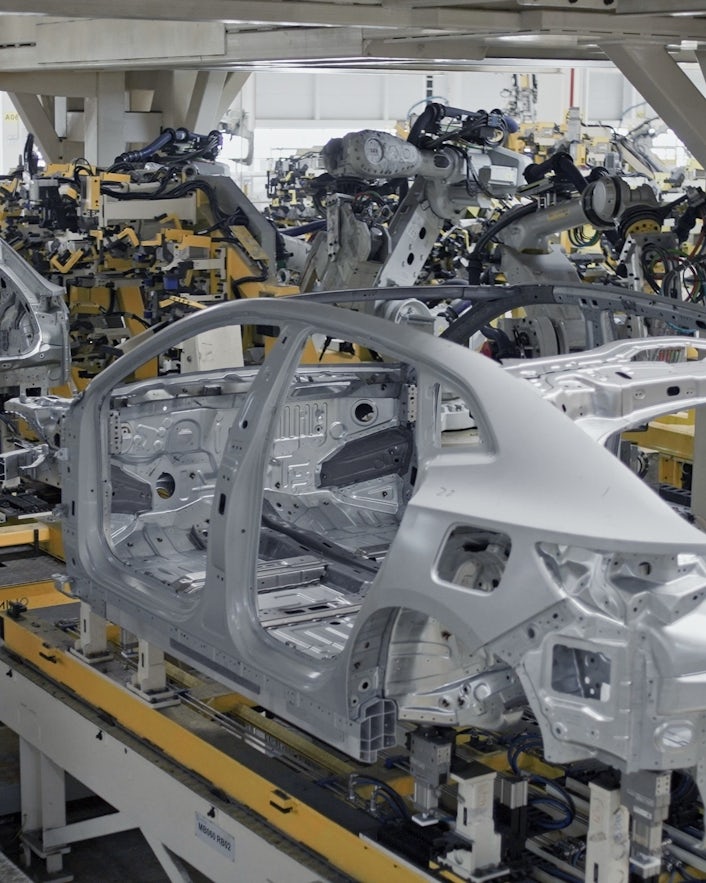
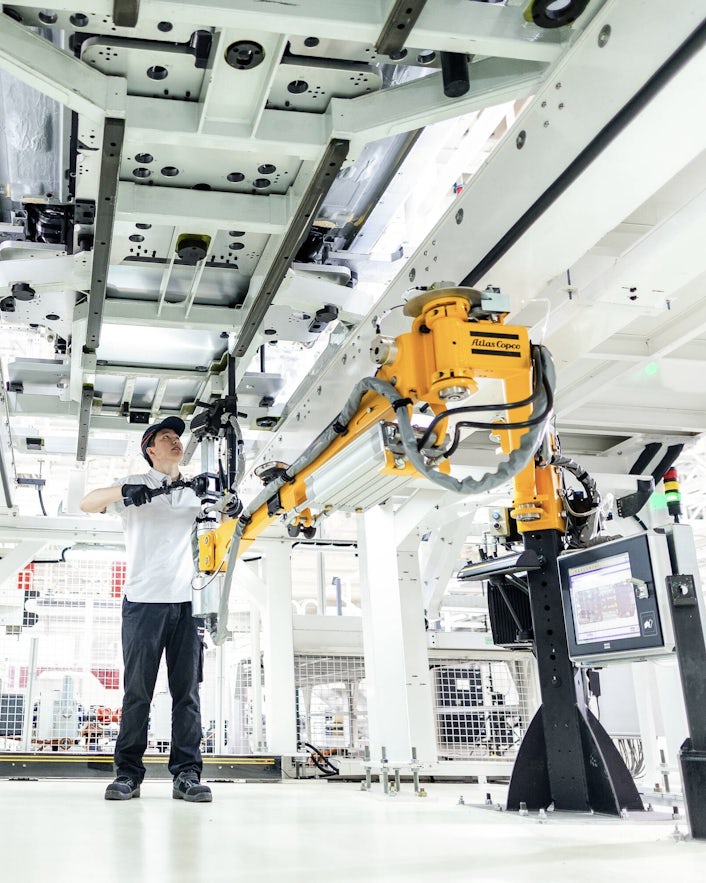
We're very confident that we can achieve carbon neutrality across all our facilities. That’s the goal.
Green power
In an industry currently shaking off its carbon-emitting past, efforts have been made to cement Hangzhou Bay’s status as one of the cleanest automotive plants in the region. From solar-panelled roofs to hydro-powered smelters, the facility ticks all the boxes expected from a facility manufacturing Polestar's lowest carbon footprint car at launch¹. “We are very serious about reducing carbon emissions across all our sites. We make sure that environmental considerations are included in pretty much every decision taken here. If you look at the progress we’ve made, we're very confident that we can achieve carbon neutrality across all our facilities in the medium term. That’s the goal," says Chunlin Zhao.
And it’s a goal that’s taken seriously. The facility comes with its own solar-powered power plant capable of producing over 48 million kWh annually. With an on-site power storage system also available, the PV plant can meet the electricity needs for a single production shift.
Global footprint
Asia isn’t the only region responsible for Polestar’s manufacturing output. Our ‘asset-light’ model – which leverages partner companies’ existing manufacturing infrastructure – has grown our global production footprint. This model of manufacturing is relatively new in the automotive world. But its flexibility provides considerable benefits.
"I think a lot of people don't realize how costly it is to set up the infrastructure required to build a car. For a young brand like Polestar to be part of the Volvo and Geely Holding ecosystem comes with some pretty important benefits. To be able to tap into the infrastructure and capabilities that are usually only available to the world's biggest automotive companies is extremely advantageous," explains Jonas Enström, Head of Operations at Polestar.
Interestingly, this approach has opened access to not just new markets but new technological advancements.
Over 7,456 miles from Hangzhou Bay lies Volvo’s Ridgeville facility. Located in Charleston, South Carolina, the site is in the middle of a $600m expansion that will see the development of the company’s first U.S. battery assembly plant. It’s also one of the locations for Polestar 3 production that is set to commence in 2024 following an additional $118m investment.
In a similar move, manufacturing of the Polestar 4 will also begin in South Korea at RKM’s Busan Plant in 2025. This unique joint venture between Geely Holding and Renault underscores the impact of Polestar's asset-light manufacturing model. “This type of deal means we can put more resources into designing and developing the best EVs in the world because we know that we can use the scale and expertise of our manufacturing partners around the world,” says Jonas.
It is an enviable position to be in; leaving us to focus on doing what we do best: designing and developing the world's most beautiful EVs.
1. Polestar 4 has the lowest cradle-to-gate carbon footprint of all our cars at launch.